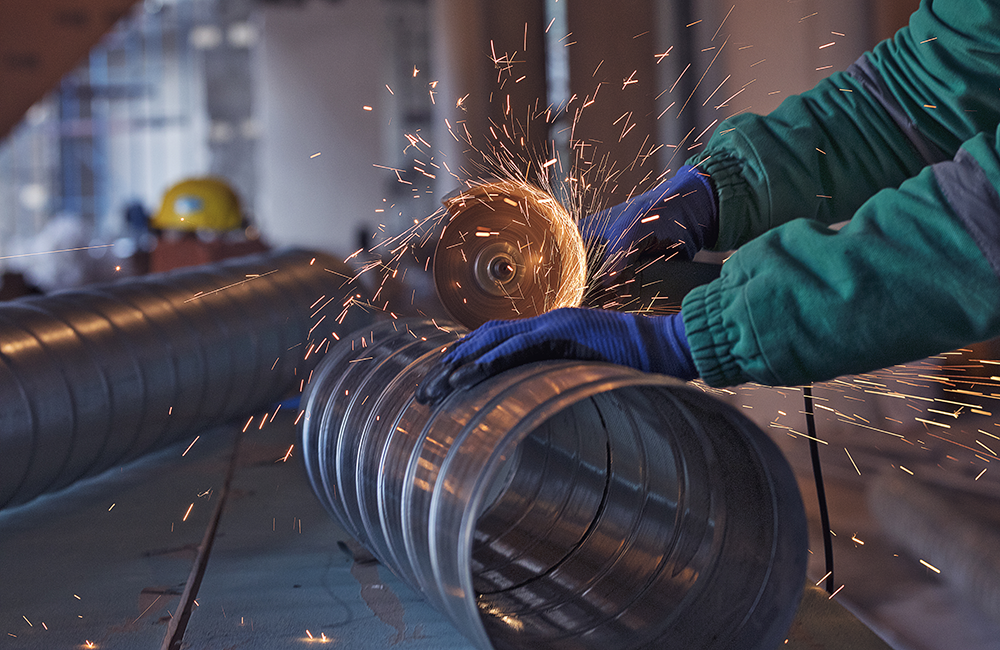
Quality Inspection Service for Mobile Phones
Blog post excerpt [1-2 lines].This text is automatically pulled from your existing blog post.
In performing sampling inspection, Veriquality follows the interntional standard ISO 2859 (or equivalent ANSI/ASQC Z1.4, NF06-022, BS 6001, DIN 40080) standard and the tables provided by it. Clients may request us to use an alternative standard if they have special requirements.
Newcomers to quality control among importers may mistakenly assume that every piece of their production should undergo inspection prior to shipment. While this approach may be advisable for high-value products, shipments with elevated quality risks, or particularly discerning customers, it may not always be necessary. For instance, Japanese customers frequently opt for 100% full piece-by-piece inspection.
Nonetheless, in some cases, conducting a 100% full inspection may not be feasible due to its high costs and time consumption, which can impact profit margins and the shipment schedule. Additionally, factories may be unwilling to accept such inspections without prior agreement.
In reality, for the majority of shipments, a random inspection with a statistically reasonable sample size is often adequate to fulfill expectations. Determining an appropriate and rational sample size, as well as an acceptance level, for such random inspections can be achieved through the use of the Acceptable Quality Level (AQL) standard. This standard aids in deciding whether a shipment should be accepted or rejected, taking into account the number and type of defects detected within the predetermined sample size.
Acceptable Quality Level (AQL): also called Acceptable Quality Limits, is defined as the maximum percent defective that, for purpose of random sampling inspection, can be considered satisfactory as a process average.
Inspection Level: The AQL tables provide for three general inspection levels and four special inspection levels. These seven levels permit the user to balance the cost of inspection against the amount of protection required.
Sampling Plan: A lot sampling plan is a statement of the sample size or sizes to be used and the associated acceptance and rejection numbers.
Critical Defect: likely to result in unsafe condition or contravene mandatory regulation or reject by import customs.
Major Defect: reduces the usability/function and/or sale of the product or is an obvious appearance defect.
Minor Defect: doesn’t reduce the usability/function of the product, but is a defect beyond the defined quality standard more or less reduces the sale of the products.
examples of Critical Defects
examples of Major Defects
examples of Minor Defects
There are two tables in AQL. The first table provides guidance on which ‘code letter’ to utilize depending on the lot size and the chosen sampling plan, like S-4, G-I or G-II (General Inspection Level II is typically the most frequently used inspection level for consumer goods), with Level III being the most stringent testing and level I being the least.
For instance, let’s say your ‘lot size’ (referring to the quantity) ranges from 3201pcs to 10,000pcs, and your inspection level is ‘II.’ As a result, the code letter will be “L.” The second table then specifies the sample size and the maximum allowable number of defects that can be accepted, based on the selected code letter. Ac refers to accepted, while Re refers to rejected. For example, using the 0/2.5/4 defect levels for a sample size of 200, the maximum acceptable limit for critical, major and minor defects will be 0, 10 and 14. Inspection with defect count beyond that limit should be considered failed in most scenarios.
Sampling plan: you will find 7 levels from G-III (highest) to S1(lowest). A higher inspection level corresponds to a larger sample size, with G-III being the highest. You can choose either level based on the following factors:
In practice, for most consumer products including garments, textiles, gifts, toys, furniture, houseware, etc., G-II are mostly commonly used and widely accepted by factories for a random inspection.
There are also cases that customers may want to determine based on the percentage % of shipment quantity rather than defined sampling levels, e.g. 10% of total quantity, that would be fine. But in that case, there would be no corresponding defined acceptance criteria and customers have to make its own judgement on how many defects are acceptable or not.
Acceptance Criteria (AQL): the lower value is chosen, the stricter the acceptance criteria is, with 0.065 as the strictest. As a common sense, you cannot expect a mass stock of 2000pcs is defect free (even for iPhone or other luxury clothes or bags), therefore it is reasonable that you should have an acceptable defect rate in mind.
For customers with little knowledge, here are mostly commonly recommended AQLs for reference:
– Critical: 0, Major: 2.5, Minor: 4.0 for inspection of garments, textiles, furniture, houseware, sporting goods, gifts, toys, etc.
– Critical: 0, Major 1.5, Minor 4.0 for inspection of consumer electronics and household appliance, etc.
It should be noted that for some products a different sampling method or acceptance limit may be more appropriate. For example, 4-point system or 10-point system other than AQL tables included here is usually adopted for fabric inspection.
Blog post excerpt [1-2 lines].This text is automatically pulled from your existing blog post.
Blog post excerpt [1-2 lines].This text is automatically pulled from your existing blog post.
Blog post excerpt [1-2 lines].This text is automatically pulled from your existing blog post.
Blog post excerpt [1-2 lines].This text is automatically pulled from your existing blog post.
Discover valuable knowledge and insights on sourcing and quality control in China and Asia. These articles are to enhance your sourcing and quality control practices in China and South Asia, providing you with practical tips and expert guidance.
Selecting the right social compliance standard: Amfori BSCI, SA8000, SEDEX SMETA, RBA, WRAP
Selecting the right social compliance standard: Amfori BSCI, SA8000, SEDEX SMETA, RBA, WRAP
Digital revolution and technical drifts have catapulted our lifestyles and standard of living into great shape. Virtual stores now allow people to shop from the coziness of their homes without the pressure of a salesperson and online marketplaces provide an innovation.
We look forward to providing a complete solution to your supply chain needs with Quality, Value, and Integrity.
Contact Veriquality to secure your imports from Asia with Product Inspection, Factory Audit and Product Testing services, Click to check our QC Services Coverage.